
Improving Condenser Efficiency with Innovative Scale Cutting Technology
North Omaha Power Station, Omaha, NE
Omaha Public Power District's North Omaha Power Station has been operating on the west bank of the Missouri River for many years. The station has four coal-fired units with a total capacity of 600 MW. Although the station is primarily baseloaded, one or more units are sometimes assigned to load following. Originally designed to burn natural gas or high Btu Kansas coal, the units have been converted to burn Powder River Basin (PRB) coal.
Turbine Efficiency Suffers
Like all power plants, a key contributor to the efficiency of the Omaha station's steam cycle are the condensers. The greater the condenser vacuum, the higher the cycle efficiency. Poor condenser performance is one of the largest causes of lost efficiency in a power plant.
Jon Hansen, plant manager, North Omaha Power Station, recalled that as the temperature of the river water rose from a low 40°F in the winter to around 84°F in the summer, the plant observed an increase in condenser back pressure of 3 to 3.5 in Hg, well above the expected target 2 in Hg. As a result, the efficiency of the turbines decreased and the plant's overall unit heat rate increased.
Another negative effect on the condensate system was that the hot well temperature increased by 10 - 15°F. in addition, because the generator hydrogen coolers used condensate as their cooling medium, the generator cooling was inadequate. Consequently, the generator's output was limited.
During a routine outage on Unit 2, scale was found in the cooling water section of the condenser. An X-Ray Fluorescence (XRF) analysis showed the scale to be calcium carbonate. This was the first time calcium carbonate deposits had been observed at the station. Additional laboratory testing showed the scale to have a deposit weight per tube of as much as 184.63 g and a deposit weight density of as much as 24.915 g/ft2. The scale caused the tube's ID to decrease from 0.944 inch when clean down to an average of 0.925 inch when scale was present.
Because of the deposit's composition and hardness, it was determined that the usual methods of tube cleaning - rod and brush, conventional gun cleaning, on-line systems, chemical injection, rotary tube cleaning systems and hydroblasting - would not be effective. The plant decided to look for alternative cleaning methods.
Conco Offers a Solution
Eventually Conco Systems was contacted and asked to examine and analyze the deposits and come up with a solution. Conco recommended the use of tube cleaners designed to break up calcium carbonate deposits in condenser and heat exchangers. Called "Cal-Busters™," each of the patented tube cleaners has two rows of four carbide wheels mounted through its circumference. The cleaners are sized to fit inside the 0.944 inch ID of the tubes with clearance.
After opening Unit 5's water box on the condenser, 25 test shots were taken using Conco's ProSeries™ 200B Tube Cleaning System. Each Cal-Buster™, using a water pressure of 300 psi, passes through the tube at up to 20 ft/sec. A tarp hung at the opposite end of the condenser collects the Cal-Busters™ and protects the water box from damage as the cleaners exit the tube.
Cleaning Method
Working around the clock with two four-man crews on 12-hour shifts, the Conco team cleaned more than 5,000 tubes per shift. Twelve or more passes were made with each tube cleaner. After cleaning the tubes with the Cal-Busters™, a heavy duty, flexible bladed Conco TruFit™ tube cleaner was used for final tube cleaning. In total, approximately 20,000 pounds of calcium carbonate deposits were removed from the condenser tubes of the four condensers.
Results and Benefits
An independent engineering firm analyzed the results of the cleaning on Unit 3 and 4 condensers. Their final report showed Unit 3 had a cleanliness of 34% before cleaning and 93% after cleaning, resulting in a heat rate improvement of 601.1 Btu/kWh. Similarly, Unit 4 had a cleanliness of 37% before cleaning and 90% after cleaning, with a heat rate improvement of 395.6 Btu/kWh. Assuming a 70% plant capacity factor, and the average 2003 market price of PRB coal of $6-7/ton, it is estimated the plant will save more than $1 million annually.
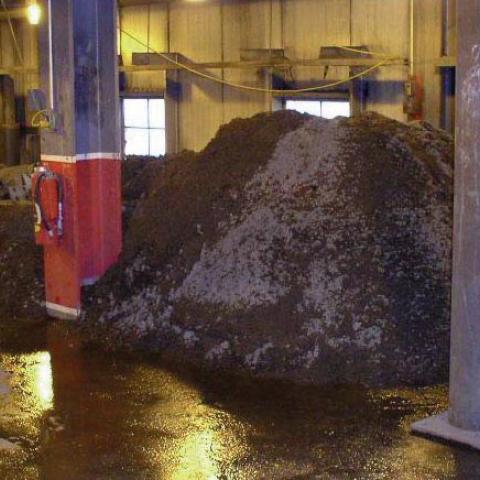
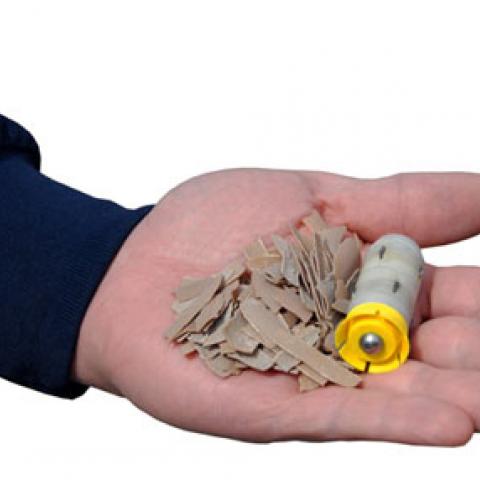
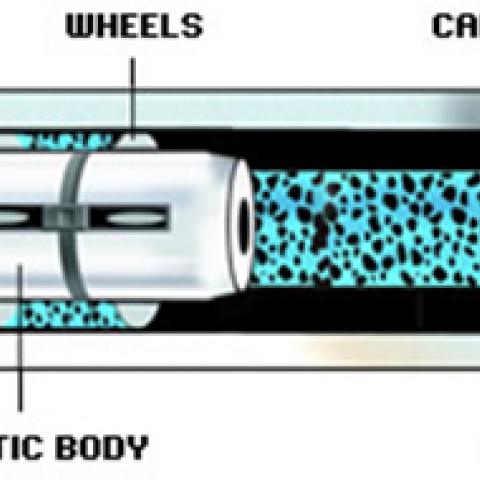
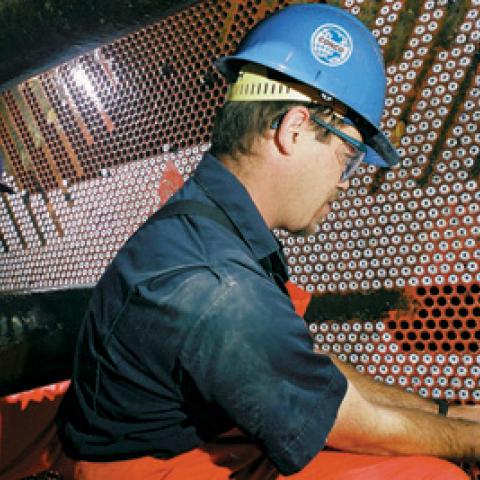
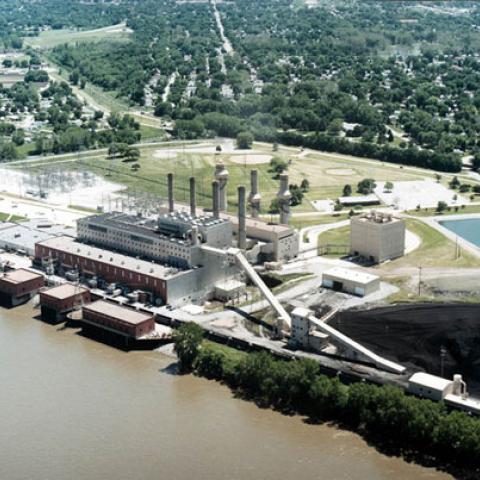